5 Costly ISO 9001 Mistakes That Ruin Certification (How to Avoid Them)
17 May 2025
ISO 9001 is the world's most popular quality management standard, with more than a million certified companies worldwide. But many companies make mistakes during the implementation phase, some of which impact resources with serious consequences, while others lead to outright failure. In this article we shed light on the most severe ISO 9001 mistakes and show you not only how to avoid ISO 9001 nonconformities, but also reduce costs and eliminate inefficiencies.
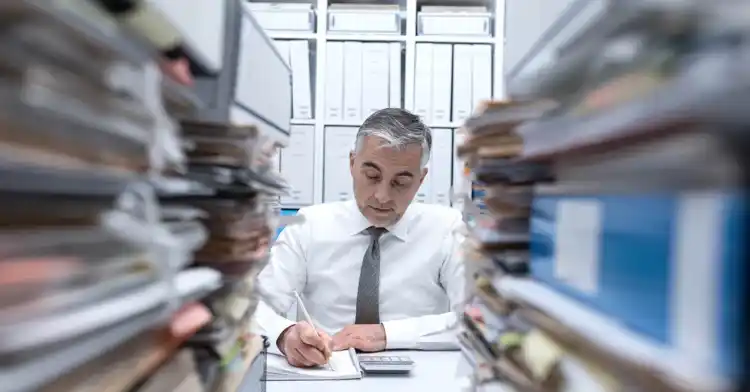
1. Costly ISO 9001 Mistake (and How to Avoid It)Seeking ISO 9001 Certification for the Wrong Reasons
ISO 9001's greatest value lies in operational improvement – not marketing. Yet many companies fixate on certification as a badge to impress clients or chase competitors, neglecting the system's power to cut waste, boost efficiency, and prevent costly errors.
The Pitfalls of Viewing ISO 9001 Certification Purely as a Marketing Tool
Consumers generally believe that products and services associated with ISO 9001 are of higher quality, so it stands to reason that advertising your certification provides a credibility boost. However, implementing a quality management system (QMS) solely for marketing purposes downplays other, more important benefits. No amount of marketing will ensure the success of your business if you're not focusing on ISO 9001 processes that produce quality goods and great customer satisfaction.
After our first conversation with 9001Simplified, we saw the value in adding controls to our system.
Abraham Couch / Environmental Painting Alternatives
Environmental Painting Alternatives (EPA) initially pursued ISO 9001 just to win a military contract – a common mistake of reactive certification. But working with 9001Simplified quickly revealed how a quality management system could transform operations.
EPA shifted from treating certification as a checkbox to using ISO 9001 as a strategic tool. The results? Streamlined processes, better communication, and stronger client relationships – proving that real value comes from implementation, not just compliance.
Their story shows how companies can turn external pressures into opportunities for meaningful improvement. Read the Case Study
The Danger of Pursuing Certification Solely Due to External Pressure
An increasing number of businesses, government departments and non-profit organizations require their suppliers to achieve ISO certification before they purchase their products and services. Government-Wide Acquisition Contracts (GWACs), as, for example, the NASA SEWP, are prime examples of sought-after opportunities that typically require ISO 9001 certification. There are also regulations for certain business activities like the NYC building code that include requirements for ISO 9001 certification.
But getting certified just because it's mandatory to access particular markets could backfire if the implementation process devolves into a quest for superficial compliance rather than an opportunity to improve operations. If your QMS fails and you can't deliver on your contractual obligations, not only will your customers be dissatisfied, there may be severe penalties and consequences.
The Risk of Implementing ISO 9001 Based on Competitor Actions Alone
If your competitors are ISO 9001 certified, you may feel you need to catch up. However, it's not enough if your actual products and services aren't as good or better than your competition. As stated already, a focus on certification simply for the sake of it won't lead to a QMS capable of reaping long-term benefits such as better quality, greater efficiency and lower costs.
The mistake of seeking ISO 9001 certification for the wrong reasons tends to result in a pro-forma quality system that's ill-suited to produce real, sustainable improvements in business operations and customer satisfaction. The opportunity costs and maintenance expenses of operating such a system make this ISO 9001 mistake particularly costly.
2. Costly ISO 9001 Mistake and How to Avoid ItLack of Top Management Support
ISO 9001 fails when leadership treats it as a "quality team project." The standard explicitly requires top management to drive the QMS – whether that's the CEO in a startup or the executive team in a corporation. Without their active engagement, certification becomes an uphill battle, and long-term benefits vanish.
Why Leadership Buy-In Makes or Breaks Your QMS
Top management's commitment isn't just an ISO 9001 checkbox – it's the backbone of a functional QMS, starting with implementation. Without active leadership from Day 1, even the best-designed systems falter: underfunded teams cut corners, employees dismiss the QMS as "corporate busywork", and misaligned priorities derail timelines. For example, a medical device startup's certification was delayed by 8 months after executives disengaged from ISO 9001 during implementation, causing duplicated workflows and audit nonconformities.
ISO 9001's clause 5.1 demands leaders “ensure integration of the QMS into business processes” – a mandate that begins at implementation. When leaders visibly champion the QMS early – approving budgets, attending kickoff meetings, and tying department goals to ISO milestones – they signal its strategic importance.
When executives disengage, it cascades: managers deprioritize training, teams revert to outdated habits, and the QMS becomes a dusty binder instead of a profit engine. For example, after leadership of a logistics firm skipped QMS reviews, approval bottlenecks caused a 25% slower order processing, costing them a key client. But when executives embed ISO 9001 into daily operations and corporate DNA – using it to mitigate risks (clause 4.1) and drive decisions – they transform compliance into a profit engine.
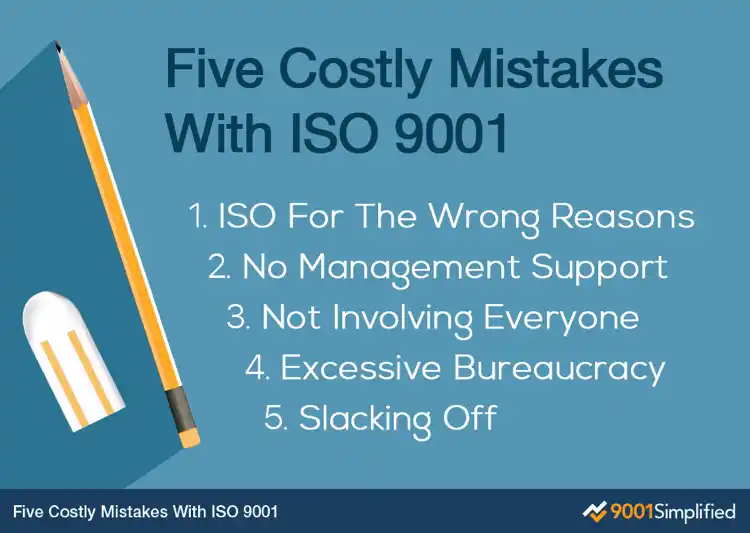
3. Costly ISO 9001 Mistake and How to Avoid ItEmployee Disengagement
A QMS built without employee input is doomed to fail. Frontline teams know where processes break down – their disengagement leads to superficial compliance, missed improvement opportunities, and audit failures.
Why Employee Buy-In Matters
A disengaged workforce doesn't just slow ISO 9001 implementation – it sabotages it. Employees who see the QMS as “corporate paperwork” will bypass new procedures, revert to old habits, and withhold critical feedback. Consider the packaging plant that rolled out updated work instructions without explaining their purpose: workers ignored the documents, assuming they were redundant. The result? Shipments piled up with mislabeled boxes, customer complaints surged, and auditors flagged a major nonconformity during surveillance.
The QMS isn't a static rulebook – it's a living system that thrives on frontline insights. Employees closest to the work know where processes crack: the engineer who spots a design flaw during prototyping, the warehouse supervisor who sees how rushed orders lead to picking errors. When their voices are absent from ISO implementation, the system becomes a theoretical exercise, not a practical tool.
In addition, auditors interview employees during assessments. If staff can't articulate how the QMS applies to their role, how the corporate quality policy affects their work, and how their work contributes to customer satisfaction, it signals systemic failure, not individual error.
4. Costly ISO 9001 Mistake and How to Avoid ItExcessive Bureaucracy
Nothing kills QMS adoption faster than pointless paperwork. While documentation is essential, bloated systems create compliance fatigue – where employees see ISO 9001 as a hurdle, not a help.
Over-documentation is the fastest way to kill a QMS. If your team needs a flowchart to navigate your flowcharts, you've already lost.
Carl Fallon / 9001Simplified
The High Cost of Over-Documentation
Many organizations make the mistake of treating ISO 9001 as a paperwork exercise, drowning teams in unnecessary forms, checklists, and procedures. This often stems from consultants pushing generic templates to inflate deliverables or internal teams over-documenting “just to be safe.” For example, a manufacturer wasted $25,000 on a consultant's 200-page QMS manual—only to discover 80% of the procedures were irrelevant to their workflows.
This over-documentation doesn't just waste time – it breeds active resistance. When employees confront a 12-page form for routine maintenance checks or a 50-step work instruction for a 3-task process, they inevitably cut corners. One audited warehouse team admitted to using a handwritten cheat sheet for inventory counts because the official procedure required 15 redundant sign-offs. The result? A dangerous disconnect between the QMS and reality, where audits expose “zombie documents” (policies that exist only on paper) and frontline teams grow cynical about ISO 9001 altogether.
5. Costly ISO 9001 Mistake and How to Avoid ItPost-Certification Complacency
Many companies treat ISO 9001 as a "one-and-done" project – only to fail surveillance audits or miss ongoing efficiency gains. Industry data shows most certified companies backslide within 18 months due to neglected QMS maintenance.
Letting your ISO 9001 certification lapse erodes stakeholder confidence faster than never achieving it. It signals that quality is optional – which is why we design systems where compliance is automatic, not an afterthought.
Greg Thompson / 9001Simplified
The High Cost of Letting Your QMS Gather Dust
Many companies treat ISO 9001 certification as a finish line – only to discover their QMS becomes a "paperweight system" within months. Without active maintenance, processes drift, employees revert to old habits, and what should be a dynamic improvement tool gathers dust. This complacency carries real consequences: auditors spot outdated documents during surveillance visits, teams waste time recreating lost knowledge, and competitors who actively use their QMS pull ahead in efficiency and quality.
The three-year certification cycle creates a false sense of security. While the certificate may last, auditors expect to see living proof your QMS drives daily decisions – not just binders of untouched procedures. Consider the manufacturer who passed their certification assessment with flying colors, only to fail their first surveillance audit when auditors found six-month-old corrective actions still unresolved. Their QMS existed on paper, but not in practice – incurring significant consultant fees bringing the QMS up-to-date and reestablishing momentum.
Conclusion
ISO 9001 certification isn't a one-time achievement – it's the foundation of a culture of continuous improvement. Avoiding these five costly ISO 9001 mistakes – from chasing certifications for the wrong reasons to neglecting post-audit upkeep – ensures your QMS becomes a profit engine, not a paperwork burden.
Ready to transform your QMS from a cost center to a competitive edge?
>> Download our fully-guided ISO 9001 Certification Toolkit
>> Contact us to book a free ISO 9001 strategy session