From Compliance to Excellence: Mastering ISO 9001 Internal Audits for Business Growth
9 March 2025
Many companies make their ISO 9001 internal audit program a police function to enforce compliance. This may satisfy ISO's requirements – but it's the loss of a great opportunity.
Internal audits are mandatory, but why not do them in a way that maximizes the return for your business? The following tips will help you improve your ISO 9001 internal audit processes and change the primary focus from identifying non-conformances to discovering opportunities for improvement.
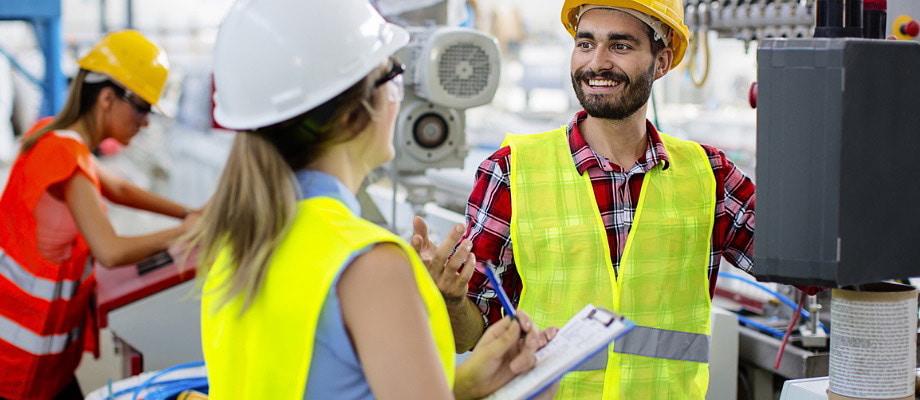
Mastering ISO 9001 Internal Audits for Business GrowthTip 1 | Involve More People
Knowledge is a key asset of your business. Systematically distributing it internally can strengthen your organization and drive improvement.
Nominate an Executive Champion
By appointing a member of Top Management as the executive champion of the internal audit program as opposed to the Quality Manager or a Lead Auditor, the organization sends a signal to employees that the internal audit program is of high importance. Nominating a single executive doesn't excuse other managers from getting involved, but it does provide a focus and single point of accountability. This champion should:
Visibly support the audit program through regular communications about the program and obtaining and assigning resources.
Facilitate a process to identify and sign off on priorities for the audits based on evidence and data (for example, customer complaints, process failures, product return rates).
Step in if schedules get off track, identify the reasons for the delay, and support solutions to get audit processes back on track.
The champion may even decide to train as an auditor and participate in audits as a way to show leadership in getting to the bottom of problems, supporting effective solutions, and drive process improvement.
Your internal audit program could prove to be the most powerful element of your quality management system.
Appoint more Internal Auditors
Rather than have a limited number of ISO 9001 internal auditors, train as many willing employees in audit techniques as you can. Not only does this approach spread the load, the organization can also plan a higher number of smaller, more focussed audits that take less time, reducing the downtime for both auditors and the area getting audited.
Training more internal auditors also results in a higher number of employees with knowledge in the requirements of ISO 9001:2015 and the organization's quality management system (QMS). In addition, the more cross-functional auditors from different parts of the organization, the higher the opportunity for cross-fertilization of ideas. And don't restrict the pool of internal auditors to more experienced employees. Train newer recruits and use audits as a way to familiarize them with relevant departments.
In a similar vein, allow employees who are interested in working in other areas to get involved with audits in that area. Examining the new section's processes will provide them with an insight into how things operate, and prepare them for new roles within the organization.
Have Mentors (Buddy System)
Once an organization has a critical mass of trained and experienced auditors, they can introduce a mentoring process or buddy system to boost the number of ISO 9001 internal auditors and support new trainees. A mentor (or buddy) provides support for the new auditor to prepare for their audits and transfer knowledge, and facilitates beneficial networks that share a focus on improvement.
The buddy system can work outside the official hierarchy. For example, someone in production might mentor someone in sales, helping the auditor to interpret the requirements of the standard for an area they may not otherwise know.
The program could be run on a purely voluntary basis or implemented as part of a professional development program with rewards and recognition for participation. Depending on the size and complexity of the organization, this improvement initiative could be coordinated by the Quality Team or as a joint effort with HR and Training and Development.
Extend to Many Auditees
It's critical that people performing tasks and activities get involved with ISO 9001 internal audits. The closer you can get to the "doing", the better. It's the people at the coalface who feel the brunt of inefficient ways of operating, and provided the audits are conducted in the spirit of helping get problems fixed rather than blaming individuals for things that go wrong, people will likely relish the chance to provide input.
Getting everyone involved with identifying areas for improvement and creating solutions is an excellent way to increase staff ownership of their role in the QMS and creates a positive environment that benefits employees and encourages them to remain with an organization long term.
Mastering ISO 9001 Internal Audits for Business GrowthTip 2 | Add Problem Solving Techniques to Auditor Skills
Training internal auditors in problem-solving techniques and encouraging them to apply them during audits will result in a deeper insight into the real or root causes of non-conformances. Solutions that address root causes will be more effective and sustainable.
Without taking the time to identify the underlying problems, the organization may find itself addressing symptoms rather than the real issues.
There are several methods that an auditor can use to analyze problems better and ultimately arrive at more effective solutions. These include Appreciation, 5 Whys, Six Thinking Hats, Flowcharts, Cause and Effect Diagrams and Mind Mapping.
Our free guide on six quality improvement techniques for more effective ISO 9001 internal audits explores these techniques and how to apply them to improve your own internal audit processes.
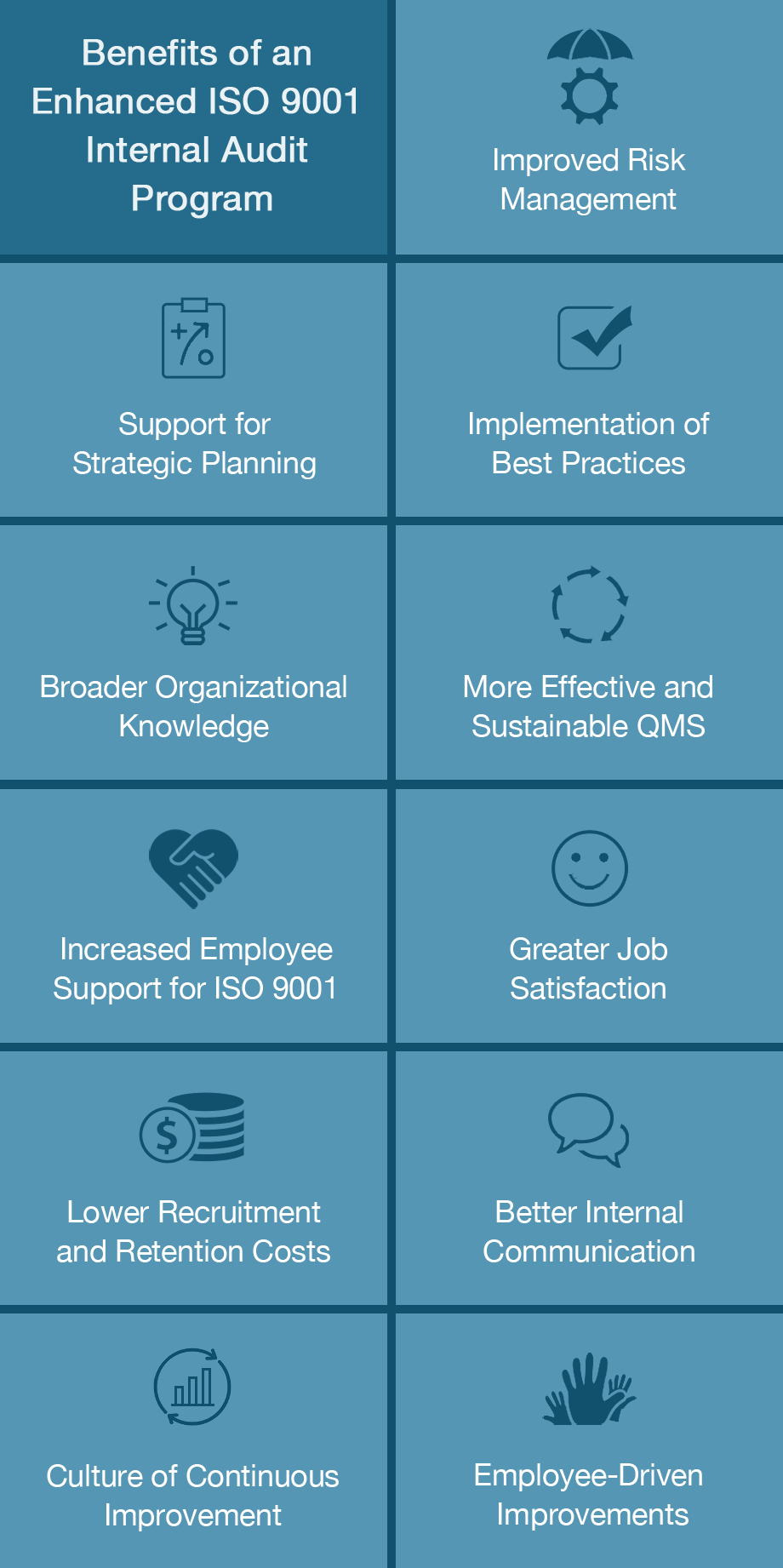
Mastering ISO 9001 Internal Audits for Business GrowthTip 3 | Go Beyond Compliance
Rather than focus solely on compliance during internal audits, make the identification of potential improvements the primary aim. Just because an area is doing what the documents say it should, doesn't mean it's the right thing to do or the best way to do it.
Moreover, if an employee isn't doing what their work instructions say they should, they might have an excellent reason for not doing so. Rather than focus on the fact that they're not complying, ask them questions like:
What frustrates you about this process?
Why are you doing this the way you are?
How would you do this better?
If you can't make the changes, who can?
Conducting process audits rather than procedural audits promotes a much stronger focus on organizational effectiveness. Instead of following an activity from input to output, a process audit tries to determine whether the tasks, resources and behaviors are managed efficiently to generate the end result, and whether the result matches the planned objectives.
The key to enabling this approach is to use a checklist that covers the requirements of ISO 9001 but can easily be customized and expanded to incorporate a process approach.
Mastering ISO 9001 Internal Audits for Business GrowthTip 4 | Use Audit Findings for Improvement Projects
When an audit reveals significant problems, use the outcome as an opportunity to involve auditors and auditees in a project to identify the root cause, devise solutions and then assess the effectiveness of changes. Rather than limit the auditor's responsibilities to carrying out the audit and follow-up of corrective actions, get them involved in helping to resolve the problem. Their expertise in quality improvement methods and the requirements of the ISO 9001 standard, along with their independence of the process and their different perspective, may result in more robust solutions than if the work area is left to find a solution in isolation.
If the problem is apparent across more than one area, create a cross-functional team to develop effective, organization-wide changes.
For example, if a review of Customer Support shows they are continually fielding complaints about incomplete orders, and a subsequent audit of the Shipping Department shows they regularly have to wait for parts to complete orders or ship multiple times to clients, then it's the perfect opportunity to form a cross-functional team. Coordinate representatives from Sales, Manufacturing (perhaps more than one area), Shipping, Logistics, and Customer Support to analyze what happens from the order right through to the shipment of the final part. By looking at the system as a whole rather than isolated processes, the improvement team can work on solutions to streamline and improve the overall customer experience.
The improvement team can map the entire process as it exists, identify weak spots and bottlenecks, collect data, identify the root cause of failures and propose solutions that take the needs and perspectives of all those involved into account.
Mastering ISO 9001 Internal Audits for Business GrowthTip 5 | Show the Effectiveness of the Audit Program
When problems are identified during an internal audit, the work area should gather baseline data before implementing a solution. Once the data has been collected, improvements can be devised, applied and their impact measured. By comparing the new measurements to the baseline, you can verify that the changes have made a positive impact. The data can then be communicated throughout the organization as proof that the audit program is providing value, consequently increasing motivation and enthusiasm for the audit program and encouraging involvement.
Providing data to back up the need for changes is one factor in keeping staff engaged with the QMS and providing increased job satisfaction.
This type of evidence-based decision making is one of the seven underlying principles of the ISO 9001:2015 standard. And even though it's not explicitly mentioned in the internal audit clause, this principle should be factored into the corrective action and follow-up stages of the audit process.
Mastering ISO 9001 Internal Audits for Business GrowthTip 6 | Recognize and Reward Those Who Contribute
Encouraging involvement in, acceptance of, and support for ISO 9001 internal audits are vital for the long-term sustainability and success of the audit program. Communicating the positive outcomes and benefits that result from the program is one way of ensuring this.
For example, if an auditor identifies a problem related to product quality and the department manager subsequently devises a solution that decreases customer complaints, the organization can communicate these results along with the methods the team used to diagnose the problem, identify the solution and verify the success. In that way, the rest of the business learns from the process and is more likely to be enthusiastic about achieving similar outcomes in their areas.
This type of recognition and reward creates a positive feedback loop and offers encouragement and incentive for everyone to play a part in the audit program and help develop a culture of improvement. Recognition might be as simple as highlighting the employees in the company newsletter or sending a note of appreciation from the CEO, right through to monetary rewards and formal awards ceremonies.
Mastering ISO 9001 Internal Audits for Business GrowthConclusion
When applying the ISO 9001 requirements for internal audits, companies can either do the bare minimum to comply with the standard or they can create a framework that adds significant, long-term value and becomes the cornerstone of their continuous improvement efforts, sustainability, and business success.
If you are struggling with a stagnant business, inject some vitality by improving your audit processes along the lines discussed above.