How to Implement ISO 9001?A Guide to Choosing the Right Approach
31 March 2025
Implementing ISO 9001 is a pivotal step toward operational excellence – but the approach you choose determines whether it becomes a strategic advantage or a bureaucratic burden. Below, we break down the three most effective methods, why they work, and how 9001Simplified delivers better results than generic solutions.
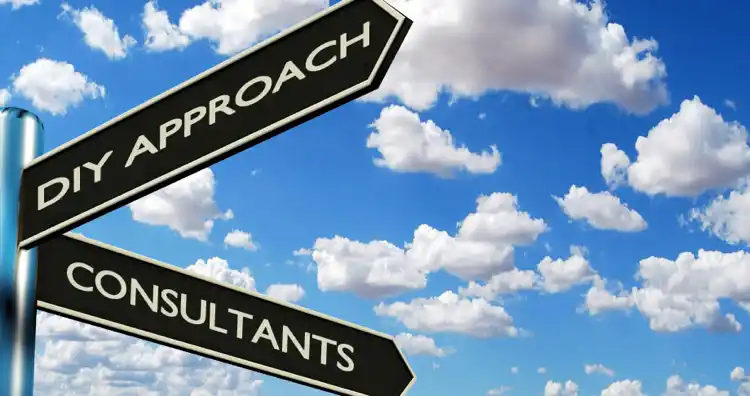
How to Implement ISO 9001?Full-Service ISO 9001 Consulting
While hiring an ISO 9001 consultant is the conventional path to certification, results vary significantly based on their approach. The most effective consultants take time to thoroughly understand your operations and thoughtfully interpret requirements to fit your business – avoiding rigid, one-size-fits-all solutions. They focus on simplifying processes rather than adding bureaucracy, and prioritize knowledge transfer over creating dependency.
When evaluating consultants, look for those who demonstrate this adaptable mindset and can provide examples of quality management systems they've designed that actually improved (rather than complicated) their clients' workflows.
Our full-service ISO 9001 Certification Service is the fastest, most reliable way to achieve ISO 9001 compliance. With this hands-off approach, we assign you a dedicated team of experienced consultants who handle every step – including documentation, employee training, internal audits, and pre-certification prep – so you can focus on running your business while we ensure seamless certification. This service can be conducted both onsite at your organization or remotely via video conferencing to reduce costs.
After our first conversation with 9001Simplified, we saw the value in adding controls to our system.
Abraham Couch / Environmental Painting Alternatives
The Challenge:
When Florida-based Environmental Painting Alternatives (EPA) faced a sudden ISO 9001 certification requirement to maintain their vital military contract, they needed more than just compliance – they needed a solution that wouldn't disrupt their production.
Our Full-Service Solution:
We provided immediate proof of progress with a binding confirmation letter to satisfy contract requirements, designed and implemented a custom QMS that integrated seamlessly with their operations, and delivered certification ahead of deadline, protecting their government revenue stream.
Who It's Best For
Ideal for leaders who want ISO 9001 done right – without diverting focus from revenue-critical work. Use cases include:
Leadership teams that can't afford to reassign key staff
Startups scaling rapidly under investor/partner requirements
Teams lacking internal ISO 9001 expertise but unwilling to accept risk
Key Benefits
Turnkey Solution: We manage the entire process – no need to decipher ISO 9001 requirements or train staff.
Fast Certification (2-3 Months): Achieve compliance in weeks, not years. Need proof for a client? We provide a signed confirmation letter guaranteeing your timeline.
Guaranteed Success: 100% of our full-service clients pass their first certification attempt.
How to Implement ISO 9001?DIY Implementation with Pre-Built Kits
Pioneered by 9001Simplified two decades ago, the DIY toolkit approach provides organizations with an affordable path to ISO 9001 certification by leveraging internal knowledge of operations and culture. Effective kits include pre-written templates that reflect lean processes, detailed customization instructions covering all operational scenarios, and training that teaches teams to intelligently adapt requirements to their workflows.
When evaluating toolkits, prioritize those that simplify processes and include clear customization examples, practical training, and coverage of all five certification phases – not just template collections.
Our guided ISO 9001 Certification Toolkit provides everything you need to implement ISO 9001 in-house, including editable templates, step-by-step guides, and training resources. Designed for self-starters, this inexpensive Do-It-Yourself approach lets you build a QMS tailored to your workflows while maintaining full control over the process.
It was very easy. The materials were very helpful and to-the-point. We just followed the instructions of the toolkit.
Maria Tsagali / AirportCreators
The Challenge:
When Netherlands-based AirportCreators needed ISO 9001 certification to qualify for EU aviation contracts, they faced two hurdles: (1) no in-house quality management experience, and (2) limited budget for consulting fees.
Our Toolkit Solution:
Using our DIY Toolkit, AirportCreators implemented a compliant QMS in just 5 months, all while maintaining their client projects. The outcome? They passed their certification audit with zero non-conformities and secured new aviation contracts within six months of certification – all without the expenses of consultancy.
Who It's Best For
Ideal for self-sufficient teams who want to own their ISO 9001 journey while saving 60-85% versus full-service options. Perfect for:
Quality managers who want hands-on documentation design and implementation
Budget-conscious businesses targeting implementation under $2,500
Teams who want to leverage intimate organizational knowledge to skip the discovery phase and build a QMS that fits from day one
Key Benefits
Complete Framework: Implement ISO 9001 successfully and error-free with zero prior experience.
Cost-Effective Certification: Achieve compliance for a fraction of consulting fees.
Expert Support: Unlimited e-consulting to answer questions as you implement.
How to Implement ISO 9001?Hybrid Implementation Approach
Originally developed to address the limitations of purely DIY or consultant-driven methods, the Hybrid Approach combines two key advantages of DIY implementation – cost-efficiency and internal process knowledge – with targeted expert guidance. This method uses your team's operational expertise to customize core documentation via a certification toolkit, while consultants provide focused support for critical phases like gap analysis or audit preparation. The most effective hybrid solutions maintain this balance: preserving your staff's ownership of the system while leveraging external expertise only when it delivers disproportionate value.
When evaluating providers, prioritize those offering truly integrated support where consultants actively work with your toolkit documents rather than disconnected services that duplicate effort.
Our Hybrid Approach blends the affordability of DIY implementation with strategic consultant support. You’ll use our ISO 9001 Certification Toolkit for core documentation and processes, while our experts provide targeted assistance for high-stakes tasks like gap analysis, internal audits, or executive training – saving 40-75% versus full-service consulting.
The Hybrid Approach provided us with the structure and expertise to overcome initial skepticism, transforming top managers from skeptics to ISO advocates.
Sarah Chen / Midwest Tools
The Challenge:
Midwest Tools faced internal resistance to ISO 9001 implementation, with leadership questioning its ROI and fearing operational disruption.
Our Toolkit Solution:
By combining our DIY Toolkit – which equipped their team to implement ISO 9001 requirements themselves – with targeted gap analysis and leadership coaching sessions, Midwest Tools transformed skepticism into advocacy, achieving certification and company-wide adoption.
Who It's Best For
Ideal for teams who want expert-participation while maintaining control – and budget – through hands-on ISO 9001 implementation. Perfect for:
Implementers who want to do it themselves but with expert safety nets for critical steps.
Growing companies requiring quick certification but can't justify full-service costs.
Teams needing consultant credibility for executive approval.
Key Benefits
Customizable Expertise: Combine our intuitive toolkit with targeted consultancy, scaling support as deadlines or complexity demand.
Fast & Affordable: Certify in 2–6 months for 40–60% less than full-service consulting.
Guaranteed Certification: Achieve 100% success with our optional internal audit.
How to Implement ISO 9001?Doing It Alone
While building an ISO 9001 system entirely in-house is theoretically possible, it often requires 500+ hours of staff time and carries significant risks:
Documentation Delays: Teams typically spend 3–6 months interpreting requirements and drafting compliant procedures from scratch.
Costly Errors: 88% of self-implemented systems require major revisions before certification (9001Simplified audit data, 2004-2024).
Lost Opportunity Costs: Diverting key staff from revenue-generating work and delaying certification benefits compounds into a significant financial burden.
What begins as an apparent cost-saving measure often becomes the most expensive approach when accounting for staff hours, delays, and audit retries.
How to Implement ISO 9001?Choosing Your Implementation Approach
Selecting the right ISO 9001 path depends on three – often interrelated – key factors. While skillful ISO 9001 implementation generally results in financial benefits, an analysis of each individual situation is needed to identify, for example, if the benefits of early certification outweigh the costs of expedited ISO 9001 implementation.
1. Urgency / Benefits of Quick Certification
Full-Service: Fastest (2-3 months; confirmation letter available)
DIY: Most flexible (3-6 months)
Hybrid: Balanced (2-6 months)
2. Budget
Full-Service: Highest upfront cost
DIY: Lowest upfront cost
Hybrid: 40-75% savings vs. full-service
3. Internal Resources / Operational Impact
Full-Service: Minimal staff time required
DIY: Have team capacity, no experience needed
Hybrid: Balance team effort with expert backup
4. Long-Term Value
Avoid "checkbox compliance" systems that become bureaucratic burdens.
Prioritize providers who:
✓ Streamline documentation (like we do)
✓ Align with your workflows (our specialty)
✓ Create efficient processes (our mission)
Need more help choosing the ideal ISO 9001 implementation approach? Request a Free Consultation.
Conclusion
Your ISO 9001 implementation approach determines everything – whether you gain a competitive edge or inherit a bureaucratic nightmare. Too many companies waste time and money on systems that look compliant but fail in practice, risking costly rework or even decertification.
At 9001Simplified, we guarantee a different outcome. Our Full-Service, DIY and Hybrid approaches all focus on what matters:
Lean documentation that eliminates busywork
Intelligent customization for your workflows
Sustainable systems teams actually use
There is no risk in trying 9001Simplified. Every solution comes with our industry-leading 30-Day Money-Back Guarantee, plus free QMS updates for DIY kit owners whenever the standard changes and a Certification Guarantee for full-service clients.
Ready to take the next step?
>> Get started with your DIY implementation today
>> Get a custom proposal for the full-consultancy or hybrid implementation